This is the third in a series of blogs about my history in the craft industry. If you missed the other posts start here.
We arrived home from the 1976 Rhinebeck craft show both elated and overwhelmed. We had wholesale gallery orders for more wall sculptures in the following 6 months than I had made in the entire short history of Wood That Works. Now what?
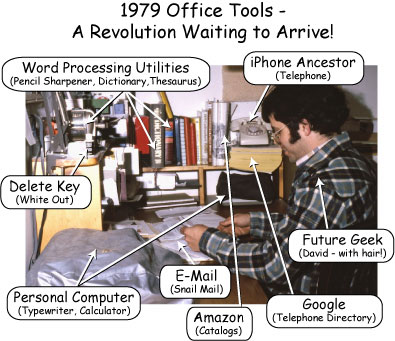
Fortunately both Marji and I are fairly organized people. We realized that we needed to learn how to run a wholesale business including (gulp) credit checks. It seemed all of our new customers wanted something called "net 30" payment terms. (Remember I had studied Physics and Marji studied art in college, not a business course between us.) The world of business was all new to us. We had to learn about invoices, packing lists, statements and something called a tickle file. Luckily we had family resources to call on.
Marji's father had quite a collection of old furniture including some ancient wood filing cabinets that were just what we needed. My mother had been an executive secretary for years. She taught us how to handle invoicing, billing, correspondence and filing techniques. My sister was an accountant and helped us set up a bookkeeping system. These seemingly mundane functions were critical to starting and running a business. The critical office equipment we had to buy included a typewriter and a calculator. I remember it as equal in difficulty to purchasing a computer today!
Marji and I had learned early on that although we loved working together we were far better off each having our own domains to control (too many bosses). I became design, production and shipping. Marji gravitated towards finance, scheduling, and marketing. Of course to make this work there was, and still is, a lot of overlap. Marji is my essential design critic and teacher. Without her, "That's nice, but have you thought of..." suggestions, my work would be far less than it is! I like to think I help in similar areas of her domain but she's probably just being polite...
The shop, all 200 square feet of it, had the tools I needed - bandsaw, drill press, router and sander. What needed to be developed were new production techniques so I could make multiples of the same design accurately and in a timely fashion. This involved a lot of invention, experimentation, trial and error but every month I discovered new tricks. There were few books and of course no Internet, so I made a lot minor mistakes, and some disasters, like when I forgot an entire production run of parts outside for the night and it rained...
To continue to part 4: Click Here